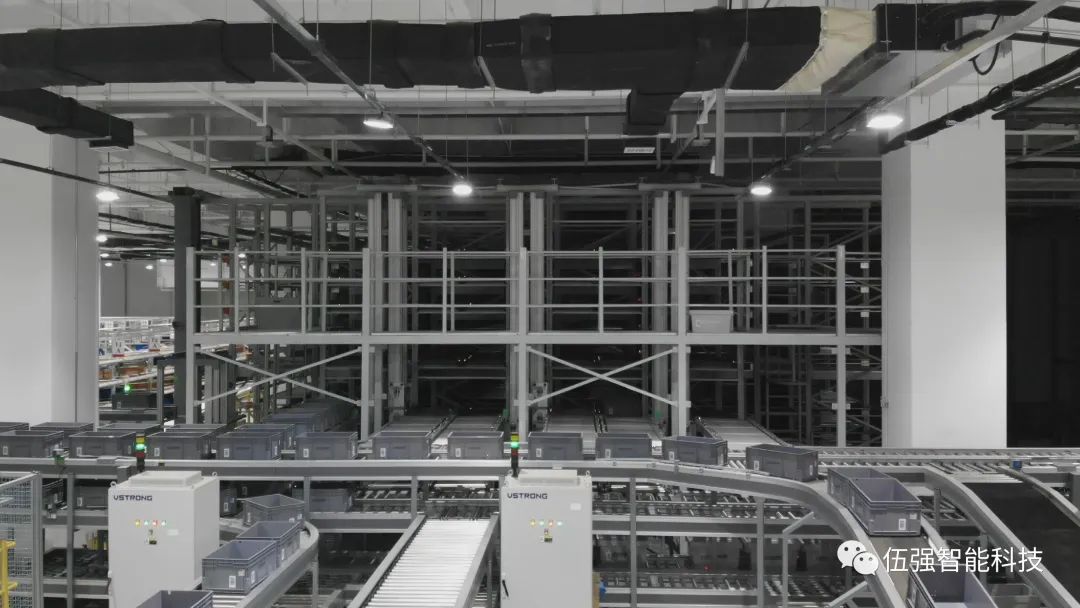
自从2013年伍强智能科技在国药集团上海医药物流系统中采用“货到人”拣选技术以后,“货到人”拣选逐渐被行业所认识和广泛接受。10年来,越来越多的用户开始采用“货到人”拆零拣选系统,“货到人”拣选技术也在不断发展、完善和创新。不过,在实际应用中,也遇到了很多问题,其中最关键的问题是拣选效率问题。本文希望就“货到人”拣选系统的设计问题展开讨论,希望对设计工程师们有所帮助。
“货到人”拣选系统的基本构成
典型的“货到人系统”,其基本构成分为以下几个部分:
1 拣选系统:即拣选工作站。拣选工作站的型式多样,其基本功能是准确完成快速拣选。一般情况下,如药品拆零拣选,一个工作站每小时拣选最大可达到500~600行,这是RF拣选的4~5倍,是电子标签拣选3~4倍。拣选工作站一般分为两层(也有采用单层的),上层为储存箱,下层为订单箱,储存箱一般采用2个位置,交替拣选,订单箱数量一般要根据具体情况确定。一般要求配置电子标签和图像辅助系统以提升拣选的准确性。
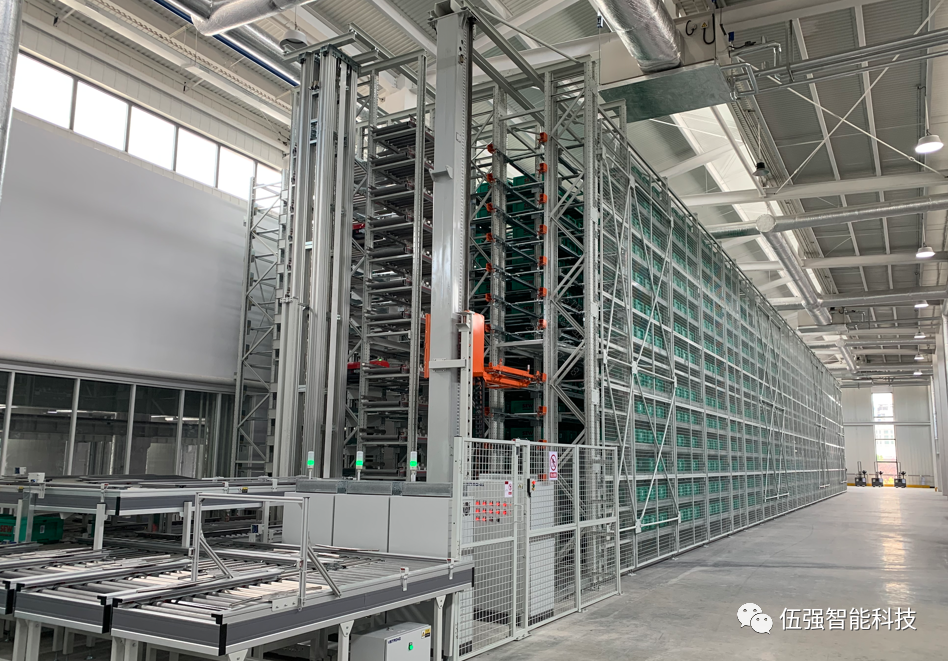
2 输送系统:一般的箱式输送线的输送能力为1000~1200箱/小时,所以,对于拣选能力500~600箱的工作站,一条输送线只能配置两个拣选工作站。如果拣选工作站的拣选能力设置为300~400箱,则可以达到3~4个工作站。这是一般的概念。对KIVA或CTU系统来说,则要根据总体输送能力来计算系统的配置,情况会复杂一些。
3 存储系统:“货到人”拣选系统的核心子系统是存储系统。以穿梭车为代表的存储系统为例,存储系统本身又分为货架、穿梭车和提升机等主要设备。存储系统的两个重要参数是储存能力(货位数)和存取能力(即吞吐能力),储存能力应根据实际需要设计,货位数由几千个到几十万个不等,很少有系统会超过100万个。存取能力则要根据订单需求来设计,并要进行严格的计算,大型系统建议采用仿真验证。
“货到人”拣选系统的基本型式
“货到人”拣选系统的基本型式主要取决于储存型式和拣选工作站型式。工作站型式多种多样,但其本质是为了提升拣选效率,往往与订单结构有很大关系。目前最常见的是两层模式(2:n,n为订单箱数),配置电子标签和图形显示以用于辅助拣选。此外还有单层模式,1对1模式,以及播种墙模式等。
关于工作站数量和每个工作站同时拣选的订单箱数量问题,其实是一个比较简单的问题,但也不是每个人都了然于胸。一般来说,工作站数量取决于每小时需要拣选的能力(行数)以及每个拣选工作站的拣选能力(行数),极少有一次拣选多行的情形发生,只有当SKU非常少的情形才会发生,但这时采用货到人拣选是不利的和不经济的。工作站拣选能力与工作站的型式、辅助工具、货物的拣选难易程度、货物大小以及每次拣选的件数有关,需要通过数据分析和实测来确定,这是一个需要动手才能确定的参数。一个工作站设计几个订单位置,牵涉的方面比较多,如订单结构就是一个非常关键的参数。既要保证拣选的连续进行,又要防止线路堵塞,这是设计的优先事项。
储存型式也是多种多样,以下是典型的几种:
1 穿梭车型:穿梭车分为双向穿梭和四向穿梭车两大类,它们又各有换层和不换层两种规格。相对来说,双向穿梭车成本低,且速度快,而四向穿梭车则更加灵活和具有柔性,具有非常强的适应性。在实际使用过程中要综合考虑。
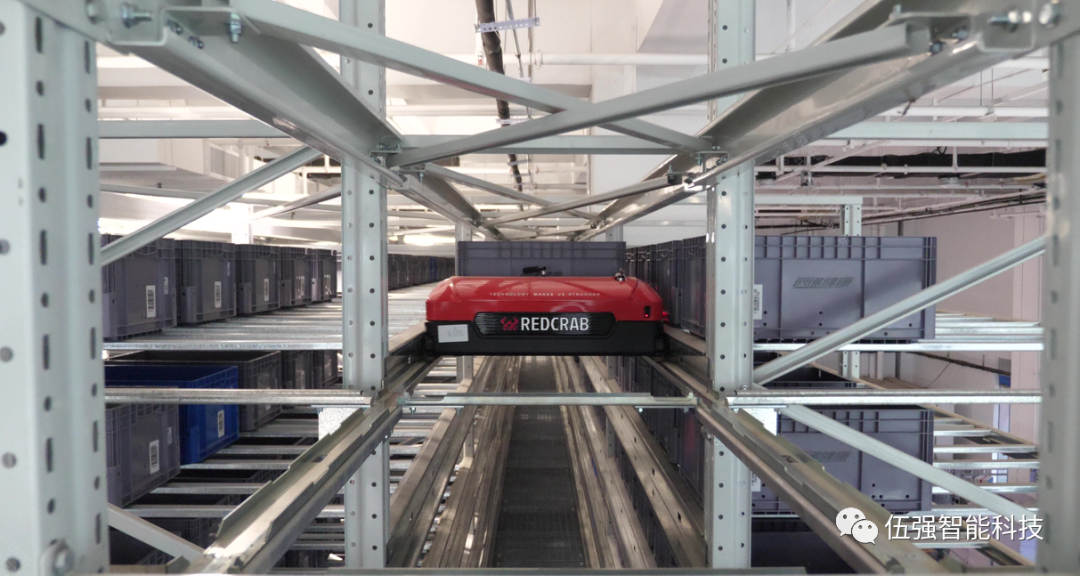
2 KIVA型(包括CTU):从根本上来说,KIVA是AGV设备的一种,采用背驼顶升式移载,是成本最低廉的一种AGV设备。正因为如此,采用大量的KIVA设备,可以弥补存取能力不足的缺点。而KIVA的高柔性,使得用户非常喜爱。目前,KIVA已经克服了高度的限制,开发出来了CTU等型式的设备,最高可达10米。这已经在很多情形下足可以与穿梭车立体库媲美了。
3 MINILOAD型:作为传统的存取设备,MINILOAD一直为人们所重视。虽然其存取能力不足是其短板,但其成本优势在很多情况下还是会帮助它成为用户的首选。通过工程师们的不断努力,一台MINILOAD设备最大存取能力已经达到200箱/小时以上,这在很多场合是足够的。
4 其它型式:如AutoStore发明了一种高密度的箱储存系统,用于“货到人”拣选,取得了很大成功。此外,各种变形的穿梭车存储系统,如垂直型穿梭车系统等,都在实际应用中发挥重要作用,极智嘉推出的POPKicking系统,则结合了KIVA、CTU和穿梭车的特点,解决了KIVA存取效率低,空间利用率不高的难题。
“货到人”拣选系统的效率问题
拣选效率是“货到人”拣选系统关心的核心问题。很多“货到人”拣选系统其实际效率与期望值相去甚远,给人们造成了很大的困惑。
影响拣选效率的原因很多,如工作站设计不合理,设备(输送机、提升机、穿梭车、KIVA等)的能力不够,设备调度混乱,系统不稳定、故障太多等,这都是表面的问题,并不难解决。我们知道,一个系统的效率决定于系统最薄弱的环节,这是比较容易识别的。
但有些问题并非如此。单机设备的能力没有问题,但系统效率却仍然达不到设计能力,有时相差很大。这样的情形在物流仓储系统中非常多,本文仅举数例问题予以讨论。
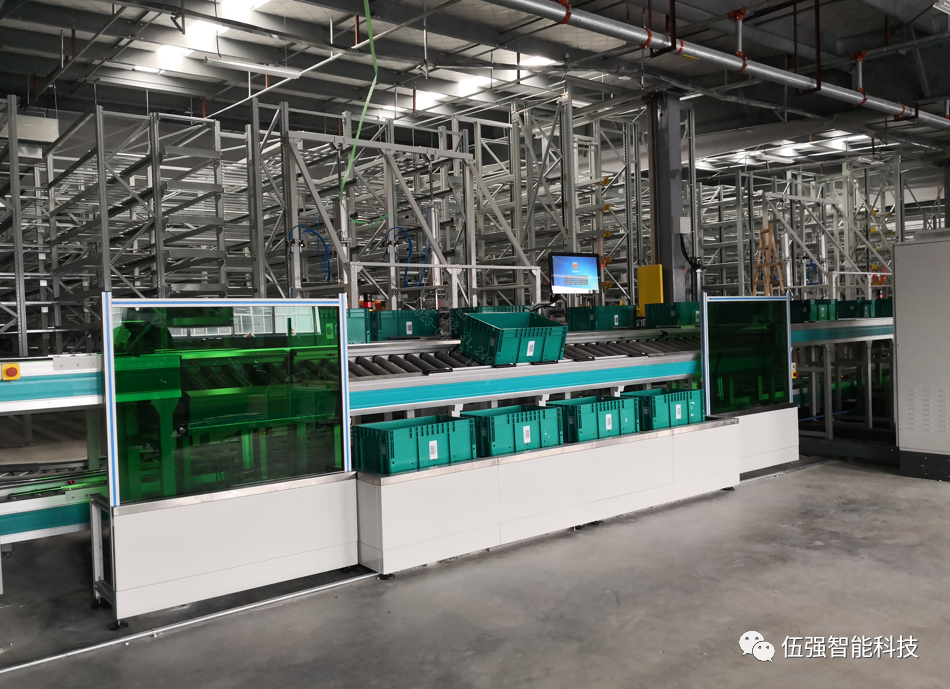
1 任务均衡性问题
在实际生产过程中,常常发现一个现象:就是在一个作业波次中,由于任务在各区的分布不均衡,导致并非是每台设备都处于饱和工作状态。Miniload、穿梭车都有这个问题。有些区域(如miniload的巷道、穿梭车的层)任务非常多,有些区域则非常少,这时,订单迟迟得不到关闭,新的订单波次下迟迟下不来,表现为系统总体效率很低。这是一个普遍现象。
解决这个问题并不容易,目前采用的方法,主要是适当减少分区的数量,在库存结构上尽量是货物的分布相对均衡,以缓解订单波次下任务不均衡现象发生的程度。
2 订单平均响应时间问题
当一组拣选任务下发后,至少需要多长时间,货物单元才能陆续到达拣选工作站,这就是订单平均响应时间问题。订单平均响应时间在系统布局完成后,基本就决定了。很多设计者不明白的是,订单平均响应时间的长短,是影响系统效率的关键参数之一。缩短订单平均响应时间,有时是非常重要的。一个任务的平均响应时间可以通过计算每一个订单行的时间得以估算,如穿梭车的平均取货时间t1,提升机平均工作时间t2,输送机平均输送时间t3,这3项时间之和基本决定了订单平均响应时间。如何优化订单平均响应时间,是设计者要考虑的关键问题。
一个基本现象是:由于订单平均响应时间过长,导致拣选工作站无箱可拣选,从而导致拣选效率低下。在实际设计过程中,要对订单结构做详细的分析。一个订单的行数n1越多,就意味着同时在线的任务数n2(n2=(k-1)*n1*p,k为一个拣选站的最大订单数,p为滞留系数)越多,允许的订单平均响应时间就越长,这样才不至于出现现场无箱可拣选的现象。从这一点看,一个拣选站台的最大在线任务数与订单平均响应时间是密切相关的。
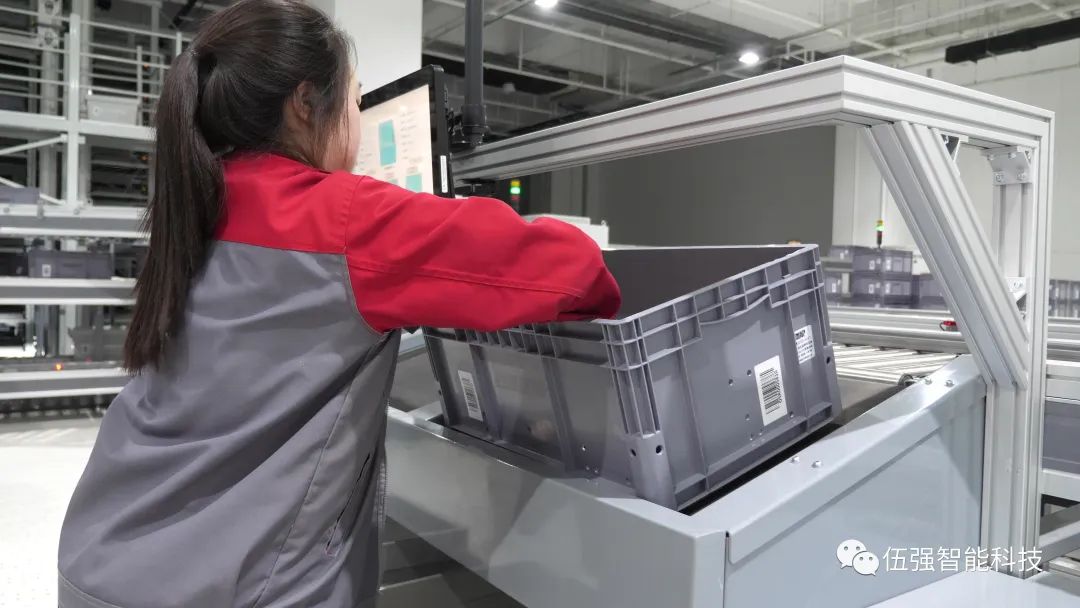
滞留系数是指线上滞留的任务数占比。假如任务下达时间间隔基本恒定(尽管实际上不是这样的),如一个拣选工作站的最大订单数为4,订单行数为4m(m是平均订单行数),则当一个新订单发起时,线上滞留的任务数大致为(0.25+0.5+0.75)m=1.5m,此时的滞留系数为0.5。
举例来说,对于一个穿梭车系统(KIVA系统也是类似的),如果t1=20s,t2=12s,t3=60s(约36米),采用2:4拣选工作站,滞留系数为0.5,则订单平均响应时间为92s,这时,如果拣选站台拣选能力为500行(箱),则至少在线任务要大于12.8个(平均每行拣选需要7.2s,92/7.2=12.8)。即在新任务发起时,如果还有至少13个以上的在线任务排队,则设计是合理的。k=4,则每个订单的平均行数要达到13/3/0.5=8.67行。有时,因为平均响应时间是基本确定的,如果订单的行数太少,则会导致系统的能力总是达不到设计值。